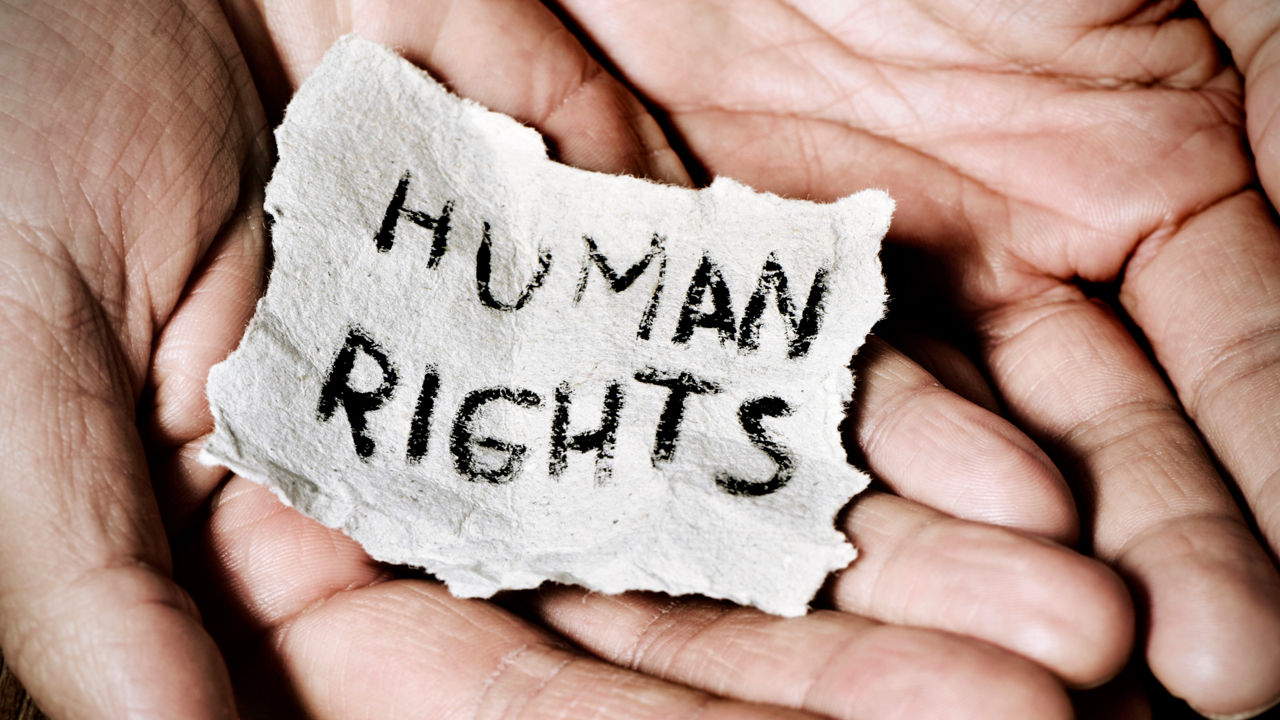
The focal point of the Audi strategy is people, in all of their many facets. As a result, observance of human rights is an integral part of responsible corporate governance, both for AUDI AG and for the entire Audi Group, in the supply chain and at our business partners.
As a global provider of premium vehicles and mobility services, Audi assumes its responsibility to create continuous economic value and jobs as well as help shape a sustainable future. But entrepreneurial action also comes with a wide range of risks. The Audi value chain is globally networked and multi-tiered. Many areas of the company are also closely integrated into the processes of the Volkswagen Group.
Audi assumes responsibility in this complex environment and has committed itself to respecting human rights. In this process, the company draws extensively on the UN Guiding Principles on Business and Human Rights. These principles are based in particular on the Universal Declaration of Human Rights (as codified in the International Covenant on Civil and Political Rights and the International Covenant on Economic, Social, and Cultural Rights), the OECD Guidelines for Multinational Enterprises and the Fundamental Conventions of the International Labor Organization (ILO).
The UN Guiding Principles on Business and Human Rights were made mandatory under the Supply Chain Due Diligence Act (LkSG) that took effect in Germany on January 1, 2023. The objective is to respect and practice human rights and environmental protection in all processes that can be influenced.
Governance
The commitment of AUDI AG to the fundamental aspects of business and human rights is anchored in the binding Audi Code of Conduct, its Compliance Management System and internal policies. The expectations placed on employees and business partners are formulated in the following documents, among others:
Audi Code of Conduct
31 missing translation: fa.download.pages, EN
3.7 MB
Statement of Principle: Respect for and Observance of Human Rights
5 missing translation: fa.download.pages, EN
180 KB
Social Charter – Declaration by the Volkswagen Group on social rights, industrial relations and business and human rights
9 missing translation: fa.download.pages, EN
3.3 MB
Code of Conduct for Business Partners
28 missing translation: fa.download.pages, EN
933 KB
Responsibility in the company
As part of the Compliance Management System, a central responsibility for the topic of business and human rights is assumed by the compliance organization of AUDI AG. This organization conducts a continuous dialogue with various functions, departments and Group coordination. Responsible supply chain management should also be noted as a fundamental element for upholding human rights in cooperation with suppliers.
Reporting
As part of the UK Modern Slavery Act 2015, Audi issues an annual statement about the measures it has taken and the management policies it has introduced to fight modern forms of slavery and creates transparency in the process.In 2024, AUDI AG reported in a Human Rights Report for the first time about its human rights activities in fiscal year 2023.
Contact
The following complaint and whistleblowing mechanisms are available for potential corporate human rights violations: