Progress is more than just a matter of technology. It begins in the mind – driven by people who are passionate about what they do, who think ahead, and who don’t let setbacks steer them off course. These people define who we are, and these are the people we need. Progress. Driven by you.
Audi Social Day
Joining forces for a good cause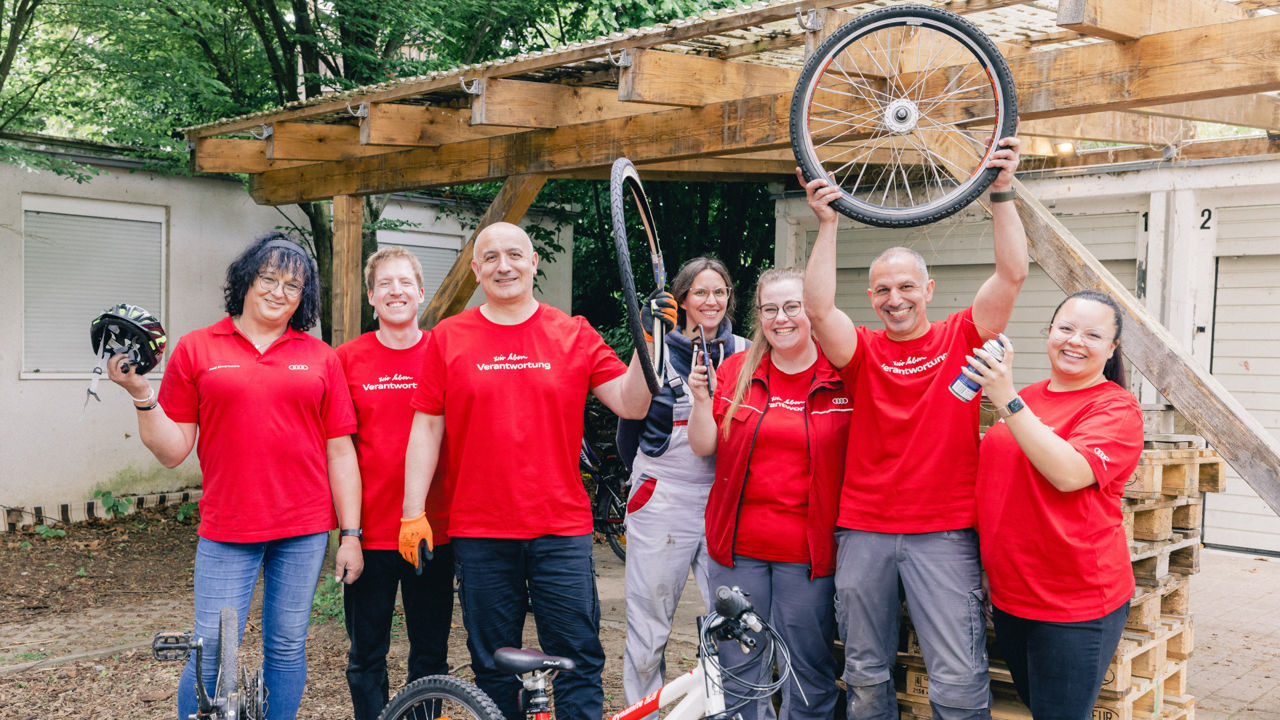