The transformation of mobility is changing the world. And we are changing with it. Boosted by a strength that has always been anchored in the DNA of our company: the strength to lead. Today, more than ever, we aspire to lead the way and inspire through premium technology. With people who share this desire and wish to join us in shaping the future together. Our Tech Stories introduce these people and show how they work hard every day - from the development of the front camera to the high-voltage battery.
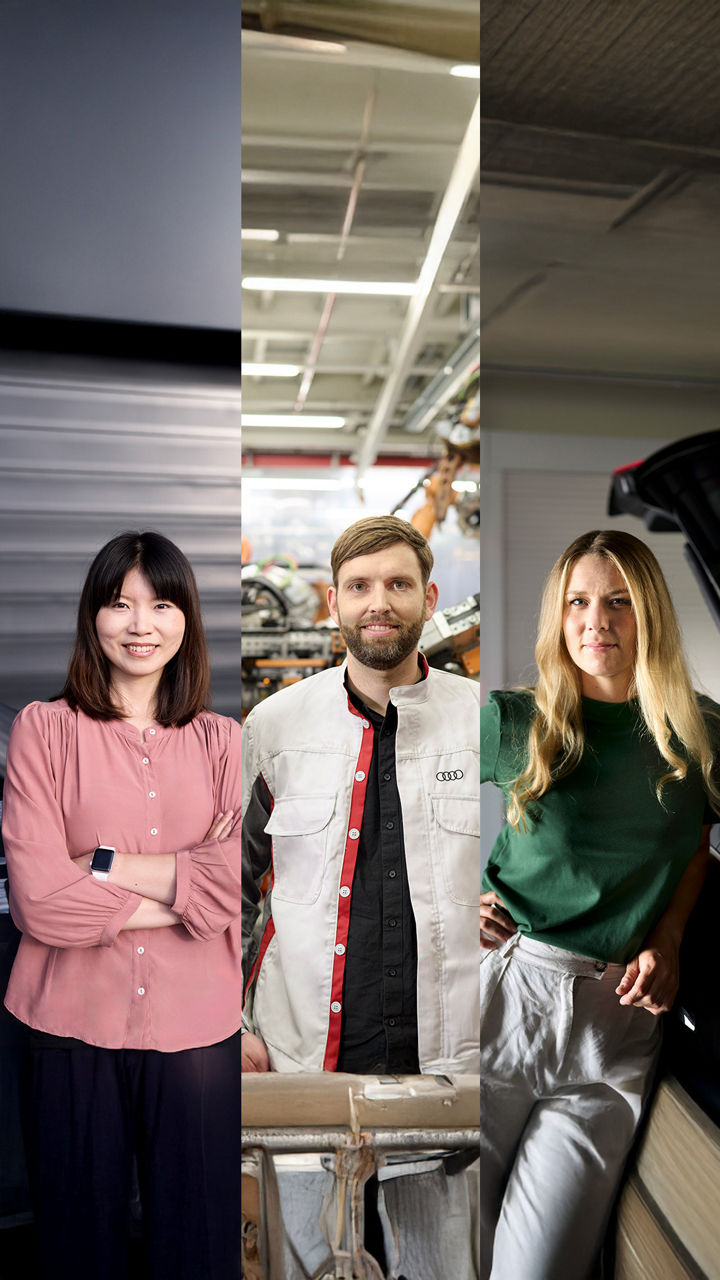
Progress is more than just a matter of technology. It begins in the mind – driven by people who are passionate about what they do, who think ahead, and who don’t let setbacks steer them off course. These people define who we are, and these are the people we need. Progress. Driven by you.
Find the right job at Audi.
Find your way to Audi
Learn more about the Audi benefits
Every individual and employee is different, and so are their lifestyles and preferences. Wherever you live, we want you to feel at home with us.