Progress is more than just a matter of technology. It begins in the mind – driven by people who are passionate about what they do, who think ahead, and who don’t let setbacks steer them off course. These people define who we are, and these are the people we need. Progress. Driven by you.
How and where is Audi using AI?
Artificial Intelligence has become an integral part of many business areas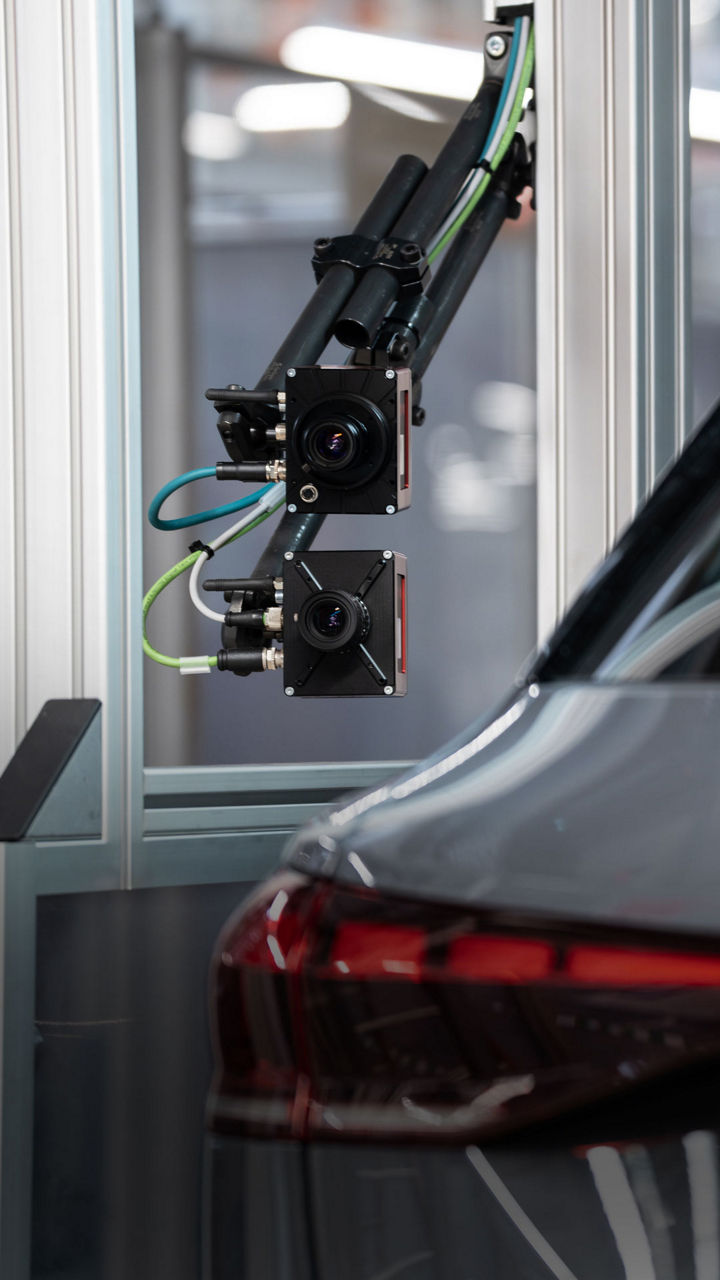
Current topics from the world of Audi
Audi Report 2024
Audi wants to shape the mobility of the future and, in the process, be the most progressive premium car manufacturer. Read the Audi Report 2024 to find out how it plans to achieve this. The combined annual and sustainability report from Audi brings together the topics of strategy, finance as well as environmental, social and governance.