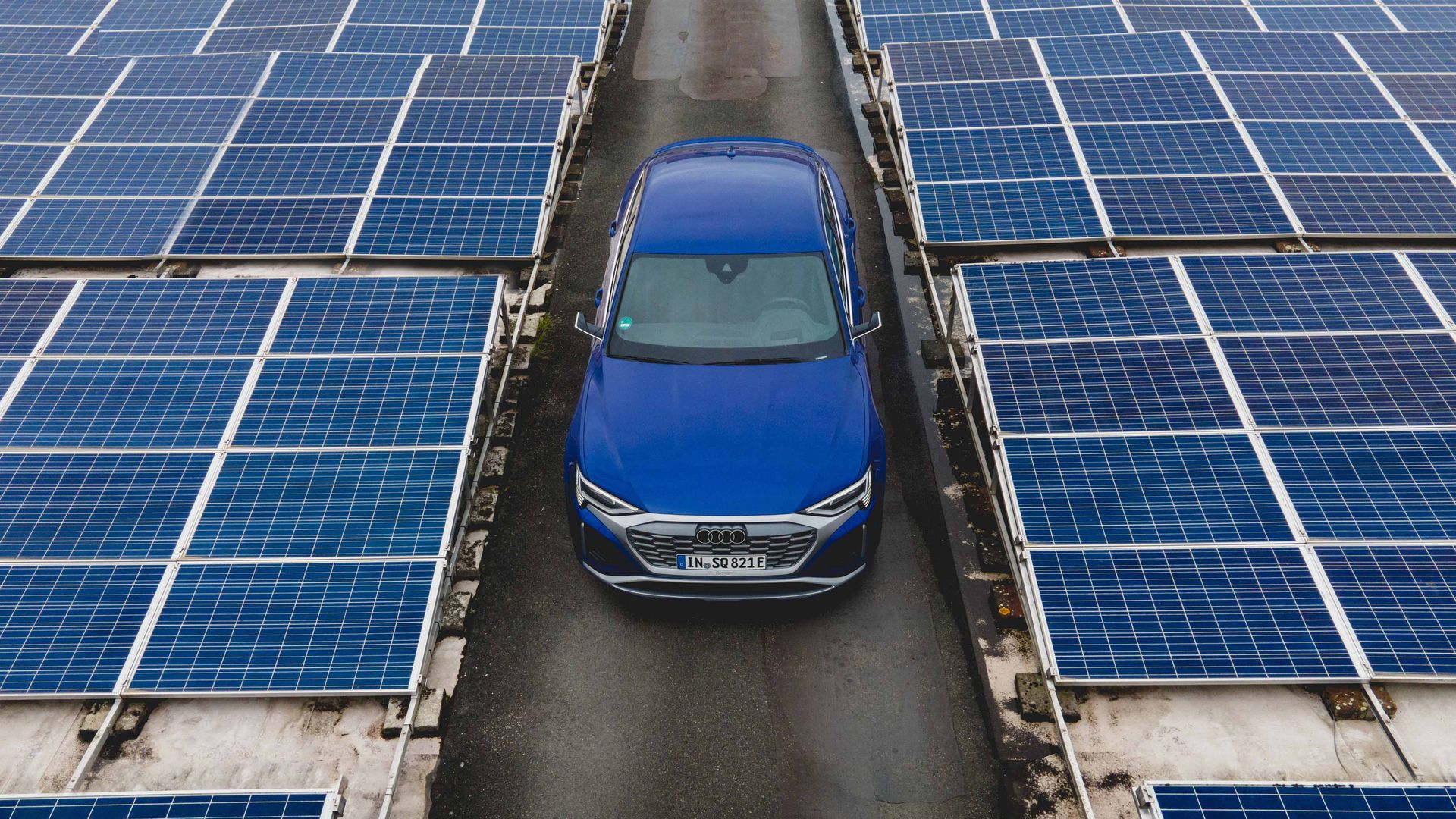
Decarbonization
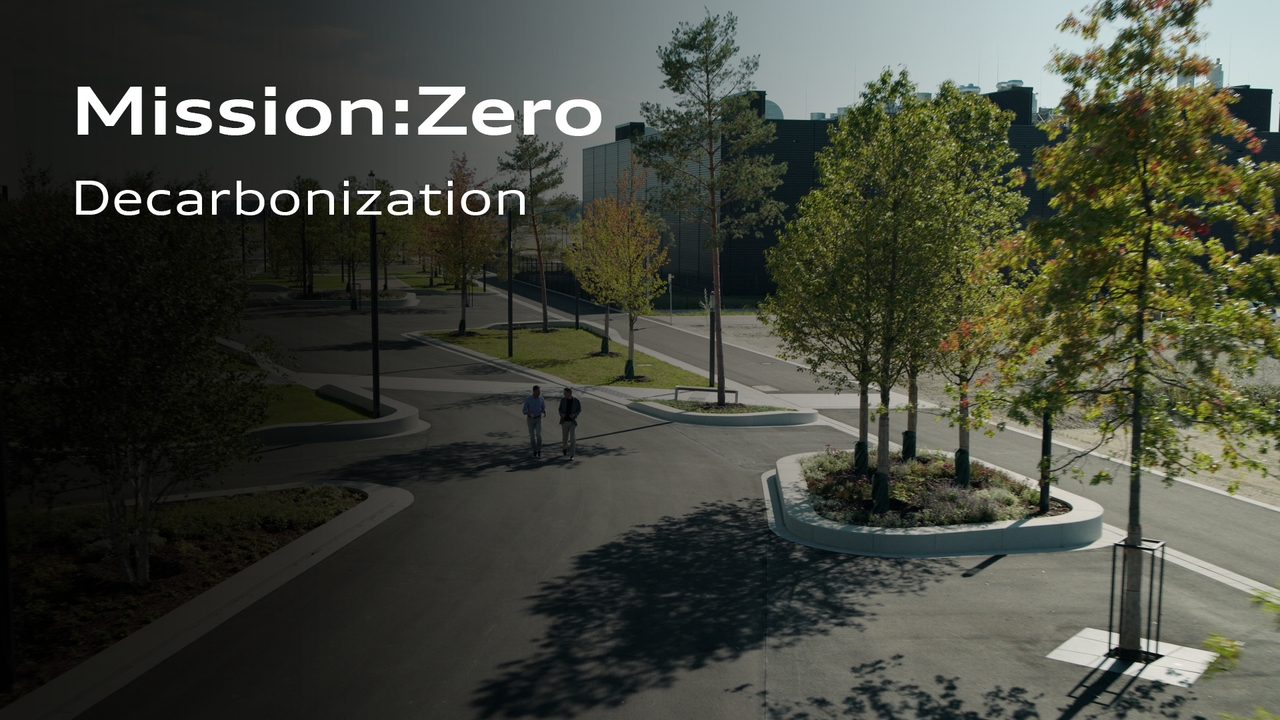
Decarbonization – that is, the reduction of CO₂ emissions across the entire life cycle of a vehicle – is an important key in sustainable business operations. It is a massive lane change being made by the whole industry toward climate neutrality. Like with every industrially manufactured product, producing a car causes emissions that arise at various points in the life cycle. Using a number of measures along this value chain, Audi is driving the transformation of its business practices toward lower volumes of CO₂ and carbon output. Two years are of particular importance for the decarbonization targets of the company: 2025 and 2050.
AUDI AG wants to become net carbon-neutral1 throughout the company by 2050. One focus is the decarbonization of Production and Logistics: the company plans to achieve the target carbon neutrality1 at Audi production sites by as early as 2025. What does it mean, exactly, that operations at all Audi locations2 will be net carbon-neutral1 by 2025? This target includes CO₂ emissions generated directly at the site (Scope 13) and indirect CO₂ emissions from energy procured through external suppliers (Scope 24).
Progress is measured via the decarbonization index (DCI) of the Volkswagen Group and within the Audi brand. The DCI is a strategic indicator for reducing CO₂. It quantifies the average emissions of CO₂ and CO₂ equivalents5 over the entire life cycle (from raw material extraction to recycling) of the Audi passenger car portfolio and is stated in metric tons of CO₂ per vehicle. It includes both direct and indirect CO₂ emissions at individual production sites (Scopes 13 and 24: 0.23 million tCO2eq) as well as all other direct and indirect CO₂ emissions in the phases of the life cycle of the vehicles (Scope 36: 45.5 million tCO2eq.).
Phase 1: decarbonization of the supply chain
Every vehicle – be it an internal combustion, plug-in hybrid or fully electric vehicle – is made up of several thousand parts that are analyzed also with regard to their CO₂ emissions. This takes the steps along the value chain for the parts into consideration, for example from the mining of the aluminum ore bauxite through to processing in the press shop. Based on the information gathered with the help of supplier companies, CO₂ reduction measures and areas of potential optimization can be identified and evaluated along the entire manufacturing process.
And Audi is aware of its significant responsibility: the company aspires to manage supply chains responsibly to generate effective results for the environment and people. Back in 2018, Audi launched the “Audi CO₂ program in the supply chain” in an effort to identify corrective actions to reduce carbon emissions jointly with suppliers. For instance, certified green electricity is used for the energy-intensive production of the battery cells for the vehicle; this is ensured via contracts with supplier companies. This commitment helps Audi optimize the existing measures and processes with respect to the pressure to act put on by investors (keyword ESG criteria).
The Aluminum Closed Loop project is one example of decarbonization in the supply chain. This alloy is made from bauxite using an energy-intensive process. To save resources and energy, the aluminum sheet cuttings generated in the press shop of Audi's production sites and in the multi-brand plant in Bratislava go back to the Blec manufacturers, who then prepare and reprocess them. Compared with primary aluminum, up to 95 percent less energy is consumed during production. Audi then reuses these reprocessed aluminum sheets in its production process. This is an approach that Audi is now applying to other raw materials.
Phase 2: Decarbonization of production
Within the “Mission:Zero” environmental program, Audi has bundled its incentives to reduce the ecological footprint in Production and Logistics. The Sustainable Development Goals (SDGs) of the United Nations and the environmental mission statement of the Volkswagen Group serve as the guiding principles for the program.
How is Audi making net carbon-neutral1 production a reality? The company has moved many levers. After all, vehicle manufacturing produces CO₂ emissions at various stages – for example the provision of electricity, heating or transportation at the plant.
Precise analyses are important as part of this, as efficiency and the right long-term decisions are crucial. And at the plant, the same thing goes as in homes: every kilowatt of energy saved neither has to be produced nor purchased. Energy-saving measures like LED bulbs and more energy-efficient drives for conveyor systems are therefore an important factor in carbon-neutral1 production.
In the medium term, the company will significantly increase its own production of renewable electricity and heat and its procurement from nearby suppliers – for example, by installing photovoltaic systems and using heat pumps to recover the waste heat from production processes. Audi will also switch to green electricity for a large share of processes that have previously relied on fossil fuels.
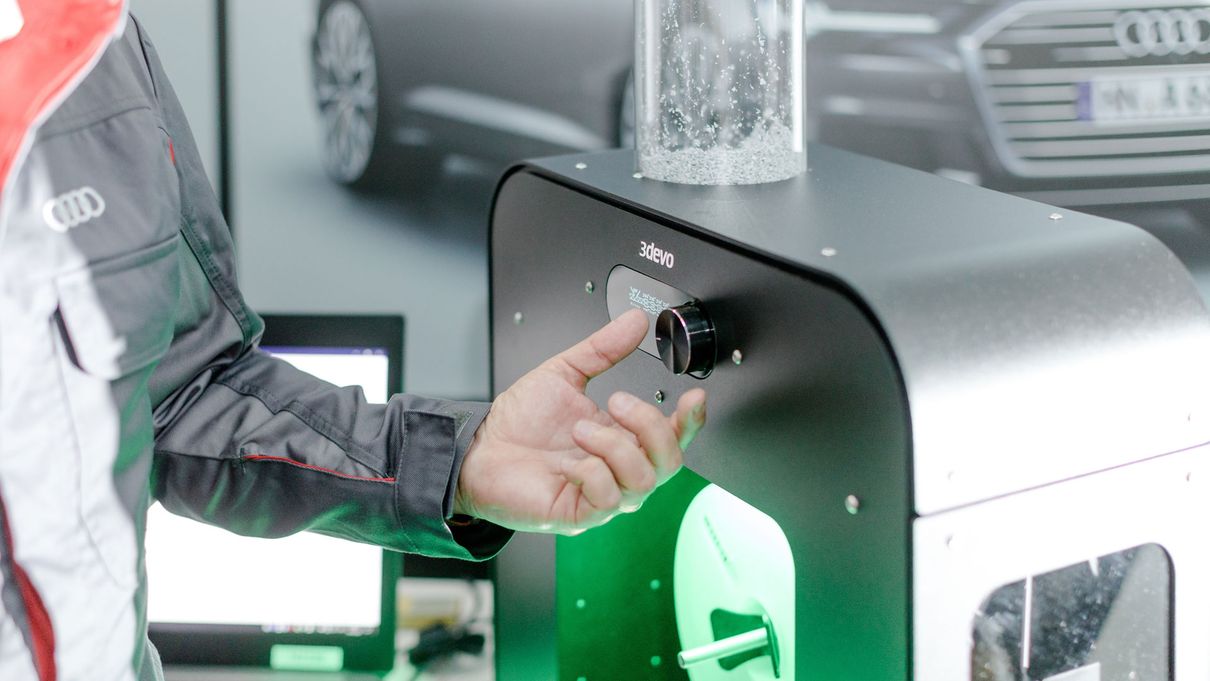
Phase 3: Decarbonization of logistics
Measures to reduce emissions in logistics are a part of the Audi “Mission:Zero” environmental program. At the heart of the efforts: together with Volkswagen Group Logistics, Audi is implementing a long-term roadmap for how transport to and from the plant can be organized in the most climate-friendly way and which transport technologies are used. The following applies in this respect: get off the road and onto the rails. The use of biogas-drive or electric trucks is under discussion in areas where the use of trucks is unavoidable.
But the “Mission:Zero” environmental program goes beyond decarbonization in Production and Logistics. The efficient use of water, resource efficiency and biodiversity are further important action areas. The vision of the company is to create circular production in which the resources used – such as plastic, water and other raw materials – are used in closed loops.
Phase 4: Decarbonization in the utilization phase
A significant portion of the CO₂ emissions of a vehicle’s life cycle are generated once the vehicle is with the customer. In light of the electrification of the portfolio of Audi vehicles, the e-tron models have the greatest potential in this regard: as an electric car, they can be operated without causing any local CO₂ emissions. And if they are also charged with green electricity, this improves the carbon footprint even more. Compared with the average electricity mix in the European Union, around half of the CO₂ emissions could be eliminated over the life cycle if a vehicle is charged using green electricity only.
Audi thus also offers its customers solutions for things like charging at home with Naturstrom sustainable electricity from Elli (Electric Life), a subsidiary of the Volkswagen Group. And when out and about, the IONITY charging network makes use of green electricity. With this joint venture, Audi is involved in the building of more than 5,000 additional fast-charging points with up to 350 kW of charging capacity at more than 1,000 locations in Europe by 2025. In addition, with the Audi charging service, Audi provides access to more than 500,000 charging points throughout Europe. And a life cycle analysis of the Audi Q4 40 e-tron shows that the dedication of Audi is paying off. If 100 percent green electricity is used to charge the vehicle during the utilization phase, the greenhouse potential is reduced by around 45 percent, thus saving approximately 14.3 tons of CO₂.
Additionally, in collaboration with multiple partners in various European countries, new wind farms and solar parks are to be built by 2025 that will collectively generate around five terawatt hours of additional green electricity. This is equivalent to the installed capacity of approximately 250 new wind turbines. The goal is to increase the proportion of regeneratively produced electricity through the partners along with the continuing increase in the share of electric cars.
Audi Q4 40 e-tron: Power consumption (combined) in kWh/100 km: 20.1–17.3CO₂ emissions (combined) in g/km: 0CO₂ emission class: A
Audi Q4 40 e-tron: Power consumption (combined) in kWh/100 km: 20.1–17.3CO₂ emissions (combined) in g/km: 0CO₂ emission class: A
Phase 5: Decarbonization in recycling
True sustainability means keeping an eye on the bigger picture – Audi is thus also optimizing the final phase of the life cycle of a vehicle: recycling.
The MaterialLoop pilot project should be highlighted in this regard – for this project, Audi and its partners are testing a closed cycle for end-of-life vehicles to find out how much material can be recycled without any loss of quality (avoiding downcycling). The MaterialLoop project provides Audi with a wide range of new insights on its journey toward implementing a circular economy. This is designed as a counter to conventional scrapping where only a small proportion of the materials were reused for the production of new vehicles. The first products, such as window panes in the Audi Q4 e-tron, prove that using recycled materials is not some crazy vision.
Every Audi vehicle contains many valuable raw materials. But for electric cars one part is of particular importance with regard to recycling: the lithium-ion battery. It is the heart and the largest part of every Audi e-tron model. It doesn’t make sense to dispose of the battery, neither ecologically nor economically, because high-voltage batteries can be put to good use even after years of use on the road.
To this end, Audi is following three approaches for this together with the Volkswagen Group:
The first is remanufacturing, which involves continuing to use high-voltage batteries in electric vehicles. The second involves so-called second-life concepts, which give batteries a second life for years outside of an electric vehicle – for instance in the fast-charging stations of an Audi charging hub. And the third is efficient recycling. This is done in Germany, for example, at a Volkswagen pilot plant in Salzgitter.
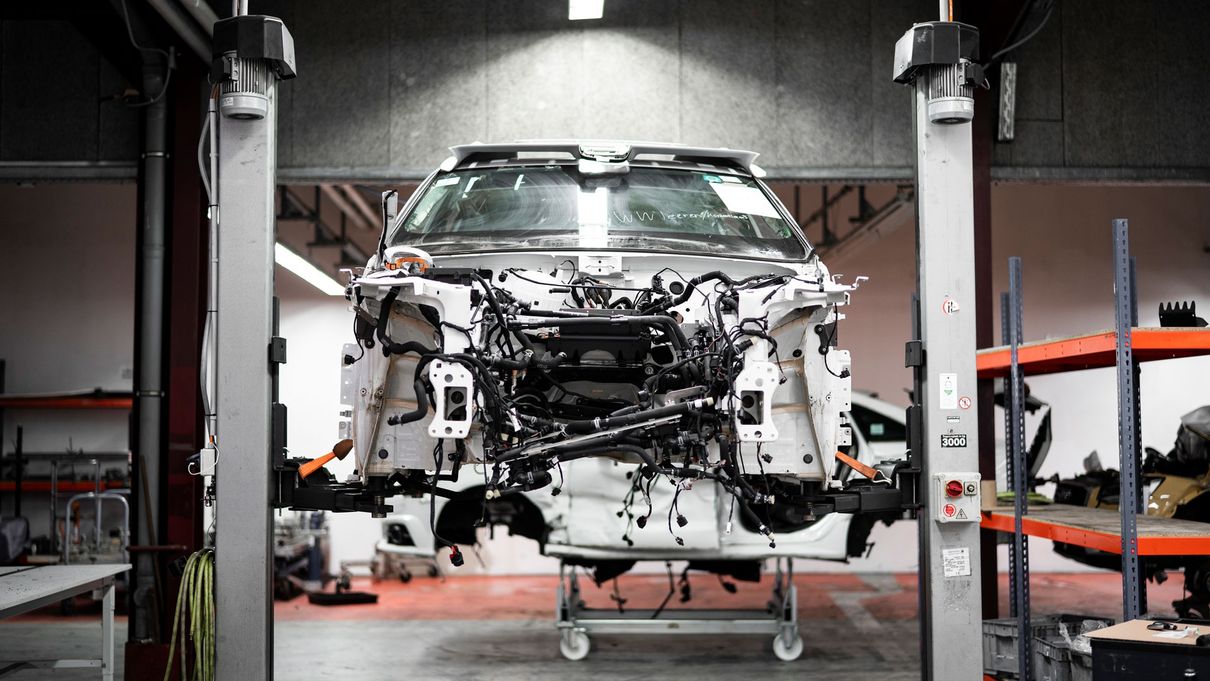